Electric Braking of DC motors
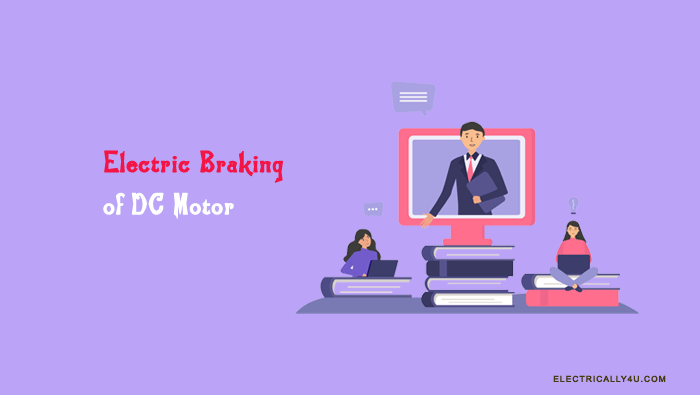
Electric braking is a method of bringing the rotating motor to rest. When the load is removed from the DC motor or when the supply is disconnected, the motor should come to rest. But there will be a delay before it stops.
The delay may be longer if the motor is huge in size and if it is running at high speed. Delay in stopping the motor may result in heavy damage to either the motor or to the product that is manufactured or to the environment. Thus braking is essential for DC motors.
Braking can be done in two ways:
- Mechanical braking
- Electric braking.
In Mechanical braking, the motor is brought to rest by means of friction in the rotating shaft. It is accomplished by adding weight to the shaft through the brake drum. The stored energy in the rotating part is dissipated in the form of heat. The disadvantage is that smooth braking is not possible in mechanical braking.
In electrical braking, the stored energy in the rotating part is converted into electrical energy. It gets dissipated in the resistance in the form of heat or it will be fed back into the supply.
There are three types of electrical braking, viz., Rheostatic or Dynamic braking, Regenerative braking and plugging.
Rheostatic or Dynamic braking
In this method, the motor is disconnected from the supply and operated as a generator by connecting across the resistance. Thus the kinetic energy of rotation is converted into electrical energy and is dissipated in the resistance. This method eliminates the electric power required to brake the motor.
For the DC shunt motor, the supply is disconnected and the variable resistance is connected across the armature. The armature current flows in the reversed direction, hence a retarding torque is produced.
As the motor speed reduces, the retarding effect decreases. To maintain the retarding torque, the braking resistance is gradually removed from the circuit.
While doing this braking operation, if there is a failure of supply, then the flux in the motor will collapse and thereby the braking effect will not occur.
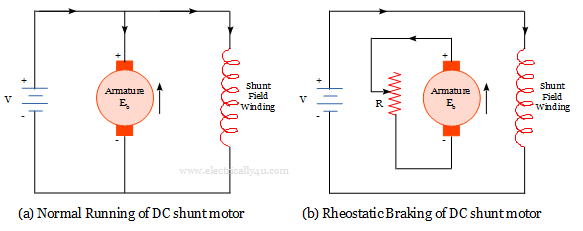
In the DC series motor, the supply is disconnected and the starting variable resistance is connected in series with the field winding. The field winding is reversed to make sure that the armature current flows in the same direction.
While doing this, the resistance in the circuit must be less than critical resistance, or else the generator will not be self-exciting.
The braking can also be done by connecting the resistance across the armature terminals. The field winding is connected to an additional resistance to limit the field current. Now the braking characteristics will be similar to that of DC shunt motor.
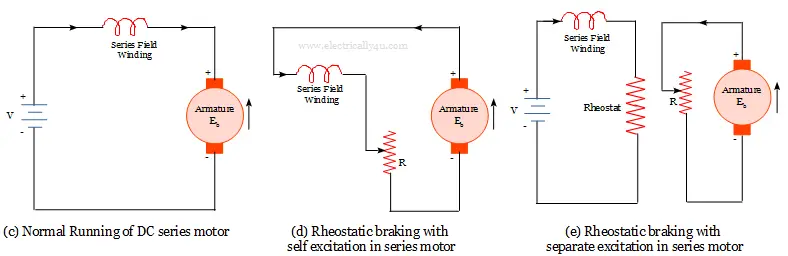
The electric braking for the compound motor is performed similarly to the DC shunt motor.
Regenerative braking
In regenerative braking, mechanical energy is converted into electrical energy. One part of the electrical energy is returned to the supply and the rest is lost as heat in windings and bearings.
For regenerative braking, the supply voltage to drop, the motor to be overexcited or the motor should run at a speed more than the no-load speed. This will make the load to act as a prime mover and so drive the machine as a generator. Hence the direction of armature current is reversed and hence a retarding torque is produced.
The torque thus produced will slow down the motor, but will not stop. Regenerative braking does not stop the motor. In the DC motor, regenerative braking can be performed without doing any modification in the armature windings.
Due to some hauling load, the speed increases above the normal speed. Due to the increased speed, the emf induced in the armature winding exceeds the line voltage. The motor starts supplying current to the line, which prevents further increase in speed.
Similarly, if the field current is increased, the induced emf will increase and exceed the line voltage. Now the motor starts supplying the current to the line, which will slow down the motor speed.
For series motor, regenerative braking cannot be done in the normal way. Because the reversal of armature current will cause the reversal of field and back emf.
Because of such complications, this braking method is not used for common industrial purposes. Instead, the windings should be modified or separate excitation must be provided to the machine.
Plugging
It is the simplest type of electric braking, also called as reverse current braking. Here, the polarity of the supply voltage is reversed, when the motor is running. It can also be done by reversing the armature current or reversing the field.
This will tend to drive the motor in opposite direction. Hence the motor will come to rest. To prevent the motor to rotate in the reverse direction, the supply is cut off when the motor stops.
This braking mechanism offers greater braking torque and is so used for rapid stopping of motors. Such a mechanism is used in controlling rolling mills, elevators, printing presses, machine tools, etc.